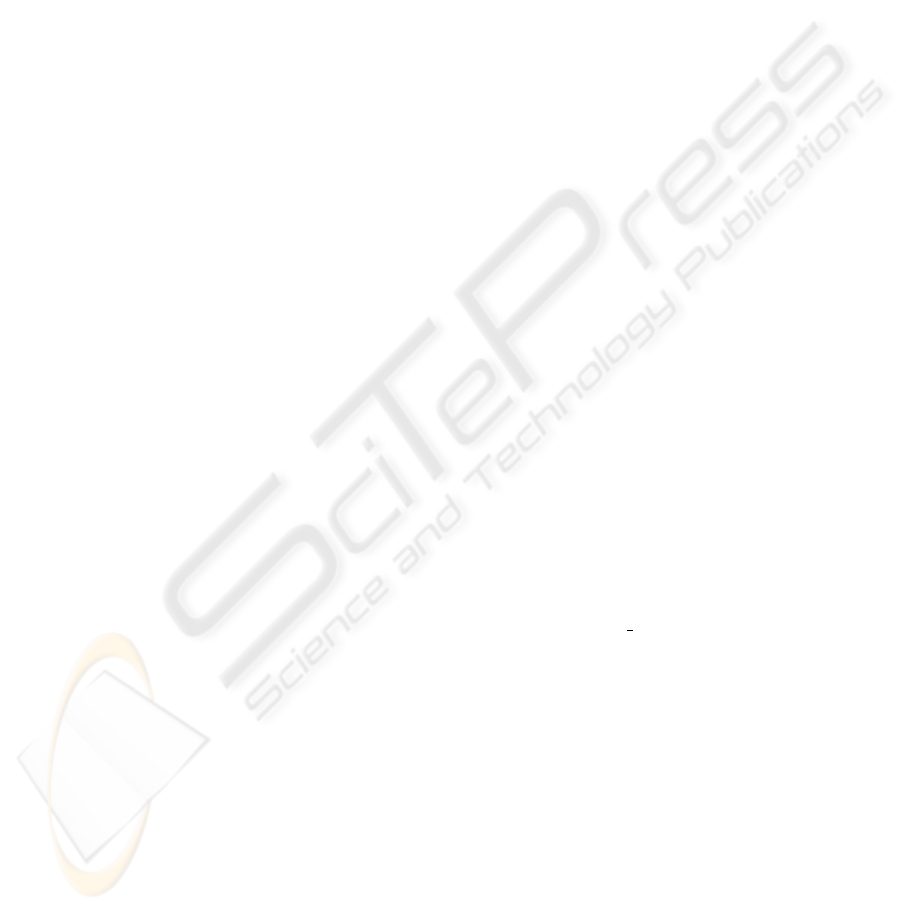
prove the suitability of the concept, we will imple-
ment an impedance controller that allows haptic in-
teraction with virtual environments. The envisaged
controller will be based on decoupling haptic render-
ing and wide area motion by optimizing manipulabil-
ity of the the haptic interface (Formaglio et al., 2005).
However, in order to achieve the goal of telepresent
manipulation with a real robotic teleoperator, more
sophisticated control schemes might be necessary.
By adding haptics to our extended range telepres-
ence system, all senses of interest will finally be telep-
resent. While users see and hear in the target environ-
ment, they receive proprioceptive feedback of their
motion and have the possibility of haptic interaction
during wide area motion. Thus the user is deeply
immersed in the target environment and eventually
identifies with the teleoperator.
This will lead to a new quality in robot teleopera-
tion as users now have a truly intuitive interface to the
robot and can fully focus on their task in the target
environment.
ACKNOWLEDGEMENTS
This work was supported in part by the German Re-
search Foundation (DFG) within the Collaborative
Research Center SFB 588 on “Humanoid robots–
learning and cooperating multimodal robots”.
REFERENCES
Bakker, N. H., Werkhoven, P. J., and Passenier, P. O. (1998).
Aiding Orientation Performance in Virtual Environ-
ments with Proprioceptive Feedback. In Proceedings
of the IEEE Virtual Reality Annual Intl. Symposium,
pages 28–33, Atlanta, GA, USA.
Bergamasco, M., Allotta, B., Bosio, L., Ferretti, L., Per-
rini, G., Prisco, G. M., Salsedo, F., and Sartini, G.
(1994). An Arm Exoskeleton System for Teleoper-
ation and Virtual Environment Applications. In Pro-
ceedings of the IEEE Intl. Conference on Robotics and
Automation (ICRA’94), pages 1449–1454, San Diego,
CA, USA.
Borro, D., Savall, J., Amundarain, A., Gil, J. J., Garc
´
ıa-
Alonso, A., and Matey, L. (2004). A Large Hap-
tic Device for Aircraft Engine Maintainability. IEEE
Computer Graphics and Applications, 24(6):70–74.
Bouguila, L., Ishii, M., and Sato, M. (2000). Multi-Modal
Haptic Device for Large-Scale Virtual Environment.
In Proceedings of the 8th ACM Intl. Conference on
Multimedia, pages 277–283, Los Angeles, CA, USA.
Bunz, C., Deflorian, M., Hofer, C., Laquai, F., Rungger, M.,
Freyberger, F., and Buss, M. (2004). Development
of an Affordable Mobile Robot for Teleexploration.
In Proceedings of IEEE Mechatronics & Robotics
(MechRob’04), pages 865–870, Aachen, Germany.
Campion, G., Wang, Q., and Hayward, V. (2005). The Pan-
tograph Mk-II: A Haptic Instrument. In Proceedings
of the IEEE Intl. Conference on Intelligent Robots and
Systems (IROS’05), pages 723–728, Edmonton, AB,
Canada.
Formaglio, A., Giannitrapani, A., Barbagli, F., Franzini, M.,
and Prattichizzo, D. (2005). Performance of Mobile
Haptic Interfaces. In Proc. of the 44th IEEE Con-
ference on Decision and Control and the European
Control Conference 2005, pages 8343–8348, Seville,
Spain.
Hoogen, J. and Schmidt, G. (2001). Experimental Results in
Control of an Industrial Robot Used as a Haptic Inter-
face. In IFAC Telematics Applications in Automation
and Robotics, pages 169–174, Weingarten, Germany.
Nitzsche, N., Hanebeck, U. D., and Schmidt, G. (2004).
Motion Compression for Telepresent Walking in
Large Target Environments. Presence, 13(1):44–60.
Nitzsche, N. and Schmidt, G. (2004). A Mobile H aptic
Interface Mastering a Mobile Teleoperator. In Pro-
ceedings of IEEE/RSJ Intl. Conference on Intelligent
Robots and Systems, Sendai, Japan.
Richard, C. and Cutkosky, M. R. (1997). Contact Force
Perception with an Ungrounded Haptic Interface. In
ASME IMECE 6th Annual Symposium on Haptic In-
terfaces, Dallas, TX, USA.
R
¨
oßler, P., Beutler, F., and Hanebeck, U. D. (2005a). A
Framework for Telepresent Game-Play in Large Vir-
tual Environments. In 2nd Intl. Conference on Infor-
matics in Control, Automation and Robotics (ICINCO
2005), volume 3, pages 150–155, Barcelona, Spain.
R
¨
oßler, P., Beutler, F., Hanebeck, U. D., and Nitzsche,
N. (2005b). Motion Compression Applied to Guid-
ance of a Mobile Teleoperator. In Proceedings of the
IEEE Intl. Conference on Intelligent Robots and Sys-
tems (IROS’05), pages 2495–2500, Edmonton, AB,
Canada.
SensAble Technologies (1996). PHANTOM Hap tic De-
vices. http://www.sensable.com/
products/phantom ghost/phantom.asp.
Stemmer, R., Brockers, R., Dr
¨
ue, S., and Thiem, J. (2004).
Comprehensive Data Acquisition for a Telepresence
Application. In Proceedings of Systems, Man, and Cy-
bernetics, pages 5344–5349, The Hague, The Nether-
lands.
Ueberle, M., Mock, N., and Buss, M. (2003). Towards a
Hyper-Redundant Haptic Display. In Proceedings of
the International Workshop on High-Fidelity Telepres-
ence and Teleaction, jointly with the IEEE Conference
on Humanoid Robots (HUMANOIDS2003), Munich,
Germany.
Unger, B. J., Klatzky, R. L., and Hollis, R. L. (2004). Tele-
operation Mediated through Magnetic Levitation: Re-
cent Results. In Proceedings of IEEE Mechatronics
& Robotics (MechRob’04), Special Session on Telep-
resence and Teleaction, pages 1458–1462, Aachen,
Germany.
A NOVEL HAPTIC INTERFACE FOR FREE LOCOMOTION IN EXTENDED RANGE TELEPRESENCE
SCENARIOS
153