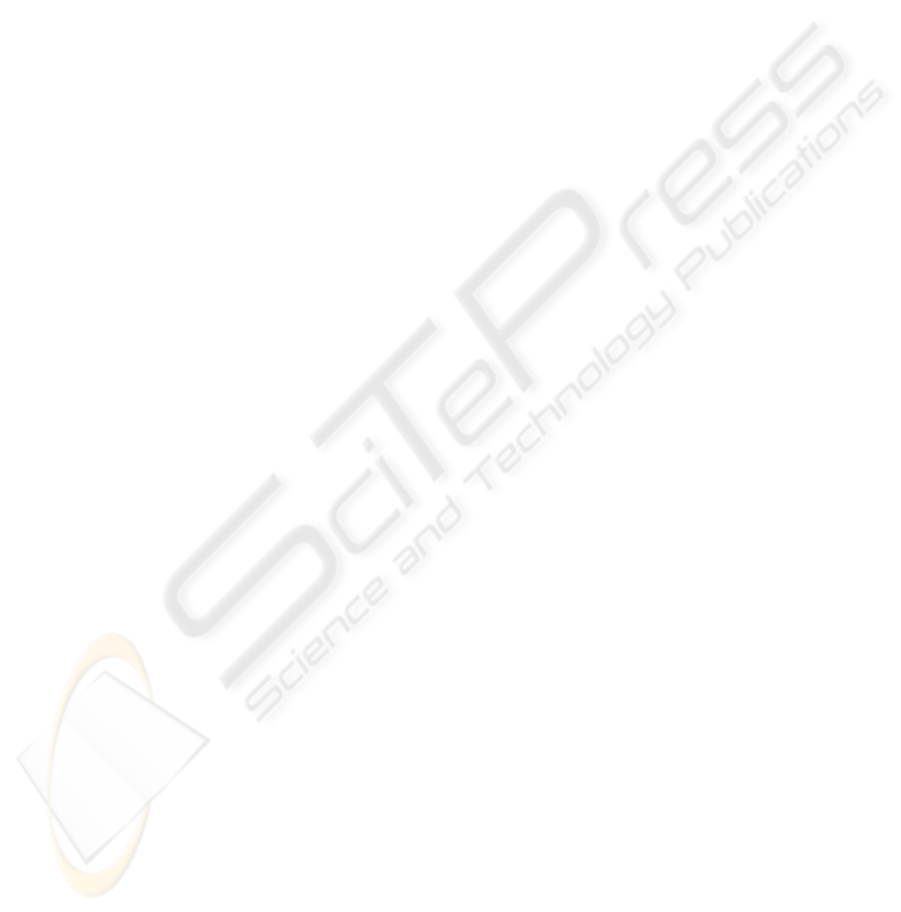
manipulator has been studied in detail. The closed
form solution to the forward kinematic is obtained
using a vector approach by considering the
individual kinematic chains inherent in such parallel
mechanisms. It is proposed to consider suitable
mapping between actuator, joint and task spaces in
both kinematic and Jacobian modeling of the
manipulator. The proposed method paves the way
for the feedback position control of the manipulator,
using a closed-form solution to the forward
kinematics and leaving out the approximation errors
inherent in numerical identification methods. It is
also shown that the forward kinematics map
provides us with some extra solutions which should
be regarded properly. Singularity analysis was also
performed using the analytic Jacobian obtained for
the mechanism. The manipulator workspace was
shown to be free of singularities due to the
redundancy in actuation. Future work will consider
Dynamic analysis of the hydraulic shoulder
manipulator.
REFERENCES
J.P. Merlet, Still a long way to go on the road for parallel
mechanisms, ASME 2002 DETC Conference,
Montreal, Canada, 2002
J.P. Merlet, Parallel Robots: Open problems, In 9th Int'l.
Symp. of Robotics Research, Snowbird, 9-12 October
1999.
S. Joshi and L.W. Tsai, The kinematics of a class of 3-
DOF , 4-Legged parallel manipulators, Trans. Of the
ASME, vol. 125, March 2003, 52-60.
S. Joshi and L.W. Tsai, A comparison study of two 3-DOF
parallel manipulators: One with three and the other
with four supporting legs, IEEE Trans. On Robotics &
Automation, vol. 19, No. 2, April 2003, 200-209.
L.Baron and J. Angeles, The kinematic decoupling of
parallel manipulators using joint-sensor data, IEEE
Trans. On Robotics & Automation, vol. 16, No. 6, Dec
2000, 644-651.
J.P.Merlet, Closed-form resolution of the direct kinematics
of parallel manipulators using extra sensors data, IEEE
Intl. Conf. On Robotics & Automation, 1993, 200-
204.
J.P.Merlet, Direct kinematics of planar parallel
manipulators, Intl. Conf. On Robotics & Automation,
Minnesota, April 1996, 3744-3749.
S.K.Song and D.S.Kwon, Efficient formulation approach
for the forward kinematics of the 3-6 Stewart-Gough
platform, Intl. Conf. on Intelligent Robots and
Systems, Hawaii, USA, Oct. 2001, 1688-1693.
Bonev, I. A., Ryu, J., Kim, S.-G., and Lee, S.-K., A
closed-form solution to the direct kinematics of nearly
general parallel manipulators with optimally located
three linear extra sensors, IEEE Trans. On Robotics &
Automation, vol. 17, No. 2, April 2001, 148-156.
B. Siciliano, The tricept robot: inverse kinematics,
manipulability analysis and closed-loop direct
kinematics algorithm, Robotica, vol. 17, pp.437-445,
June 1999.
A. Fattah and G. Kasaei, Kinematics and dynamics of a
parallel manipulator with a new architecture,
Robotica, vol. 18, pp. 535-543, Sept. 2000.
O.Didrit, M.Petitot and E.Walter, Guaranteed solution of
direct kinematic problems for general configurations
of parallel manipulators, IEEE Trans. On Robotics &
Automation, April 1998, 259-266.
B. Dasgupta, T.S. Mruthyunjaya, The Stewart platform
manipulator: a review, Elsevier Science, Mechanism
& Machine theory,2000,15-40.
Hayward, V. and Kurtz, R.: Modeling of a parallel wrist
mechanism with actuator redundancy, Int'l. J.
Laboratory Robotics and Automation, VCH
Publishers, Vol. 4, No. 2.1992, 69-76.
Hayward, V.: “Design of a hydraulic robot shoulder based
on a combinatorial mechanism” Experimental
Robotics III: The 3rd Int'l Symposium, Japan Oct.
1994. Lecture Notes in Control & Information
Sciences, Springer-Verlag, 297-310.
Hayward, V.: “Borrowing some design ideas from
biological manipulators to design an artificial one” in
Robots and Biological System, NATO Series,
Springer-Verlag, 1993, 135-148.
H. Sadjadian and H.D. Taghirad, Numerical Methods for
Computing the Forward Kinematics of a Redundant
Parallel Manipulator, IEEE Conf. on Mechatronics
and Robotics, pp 557-562, Sept. 2004, Aachen,
Germany.
KINEMATIC AND SINGULARITY ANALYSIS OF THE HYDRAULIC SHOULDER: A 3-DOF Redundant Parallel
Manipulator
131