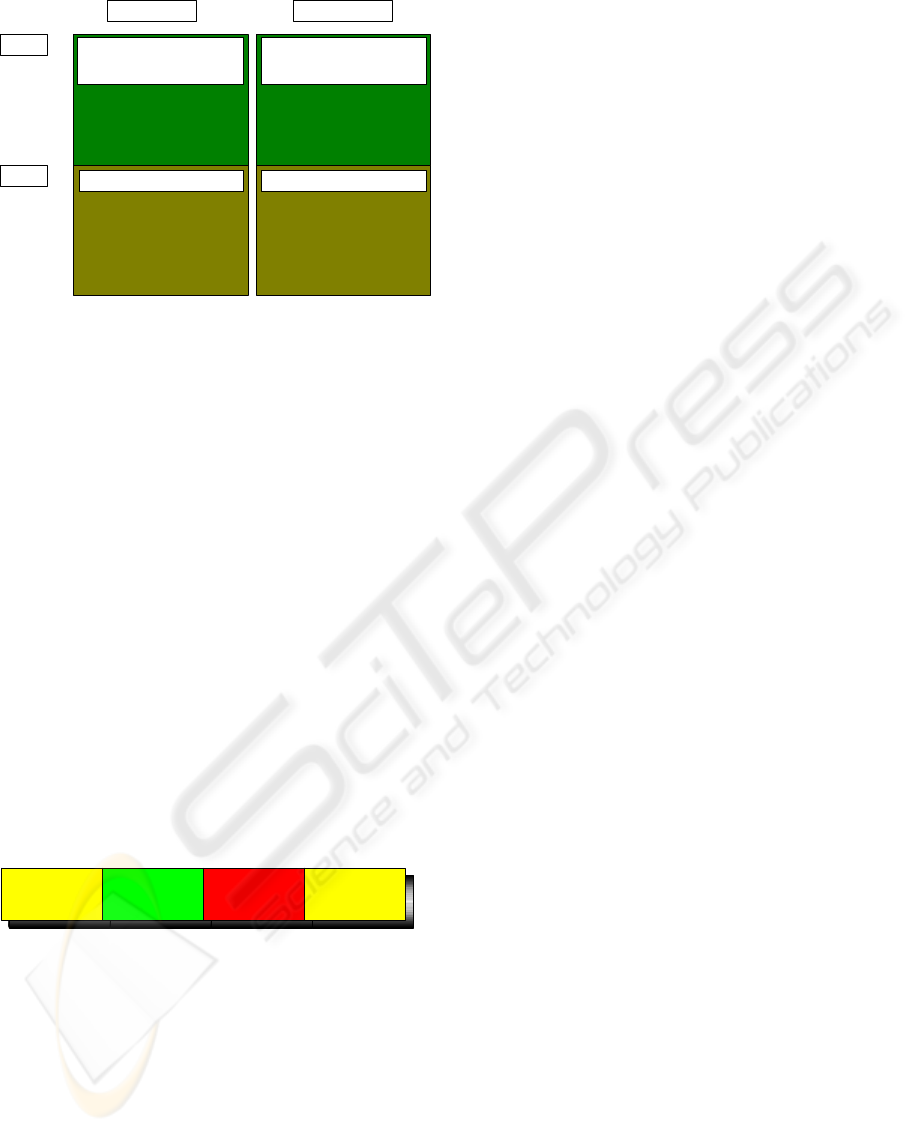
Figure 6: Memory mapped I/O card
As shown in Figure 6, the PC-Card is designed as a
memory card with an address range of 64 kByte In
the lower part of this range, the built-in flash
memory is selected and provides two types of
information. The first, called Attribute Memory,
enables the PC-Card to be used in combination with
an operation system. A special data structure (CIS,
Card Information Structure]) located at the address:
0x0000 describes the card’s characteristics in a
standardized way (PCMCIA, 1989). One of the
characteristics of this PC-Card is the command
register at the location: 0x80000, which is used to
set the gate time of the period measurement. The
second kind of information is placed in the common
memory address area. An optional file system
located at the address which is defined in the
attribute memory can be used to store additional
information (see chapter 4.5). Above the address:
0x80000, an eight-byte data structure stores the
measurement results. Details of the structure are
shown in Figure 7.
Figure 7: Data structure of the period measurement
Every time a measurement cycle is completed, the
identifier is automatically incremented. The result of
the measurement is calculated by dividing the period
counter by the clock counter. Synchronization of the
reading and the measurement logic is done by
evaluation of both identifiers. Only if these
identifiers are equal, the data structure is accepted to
be consistent.
3.5 Software Interface
A PC-Memory-Card type was developed for this
application. Such cards do not require specialized
software drivers, because they are detected correctly
by modern operating systems. Access to the memory
mapped data registers is implemented using a file-
mapped-I/O method. A special file image is placed
in the Flash-Storage with a total length of 0x80000
Bytes. In this image the last file in the directory
structure is not a real, but a virtual data file. Within
the FAT (File Allocation Table) the content of this
virtual file is linked to the data registers in the CPLD
outside the Flash-Storage area. The software running
at the host computer can now easily access the
measurement data by issuing a read command to this
file. Calibration data and parameters as well as
customer specific algorithms are stored at the host.
The application program uses this additional
information to calculate the density from the
measurement data.
The remaining files on this image are real data
files. They hold the necessary information
concerning the PC-Card (documentation, evaluation
program etc.).
4 CONCLUSION
The application of the described PC-Card-Interface
shows excellent results in the field and offers for the
evaluation of external density cells a convenient
solution which is capable to interact with PCs,
PDAs, modern laboratory density meters and
evaluation units (Anton Paar GmbH, 2005). The PC-
Cards CIS informs the host about the file system and
is therefore mapped as an exchangeable volume
without the need of special drivers. Due to the file-
mapped I/O structure, only simple file access is
required to get the measurement data.
REFERENCES
Leopold, H., Eichberger B., 1993, Ein Sensor für die
Dichte heißer Flüssigkeiten, Tagung Mikroelektronik,
Berichte der Informationstagung ME 93, Pages 102-
106, VDE-Verlag, Wien
Röhrer, R., 1989, Proceedings on the 2
nd
intensive course
on : „Programmable Logic Device“, pp.91-132, Cluj-
Napoca, Romania
Anton Paar GmbH, 2005, www.anton-paar.at
Kontron, 2005, www.kontron.com
PCMCIA, 1998, Personal Computer Memory Card
International Association, www.pcmcia.org
FLASH FLASH
CPLD CPLD
COMMON MEMORY
ATTRIBUT MEMORY
0x80000
0x00000
optional FILE Structure
optional CIS (Card Information
Structure)
DATA REGISTER COMMAND REGISTER
Identifier_1
(1 Byte)
Period Counter
(2 Byte)
Clock Counter
(4 Byte)
Identifier_2
(1 Byte)
HIGH TEMPERATURE DENSITY MEASUREMENT CELL WITH A PCMCIA-INTERFACE
319