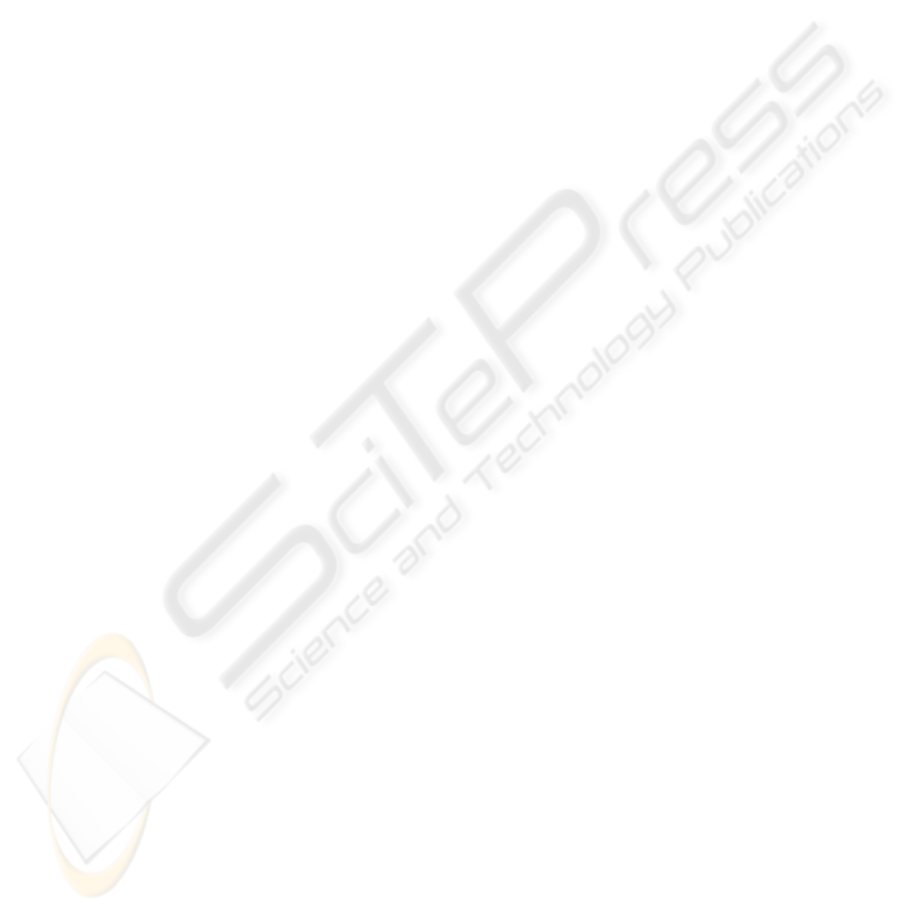
D
YNAMIC HYSTERESIS MODEL DERIVATED FROM LuGre
MODEL
Sinuhe Benitez
CITEDI-IPN
2498 Roll Dr. 757 Otay Mesa San Diego, California, 92154 USA
Leonardo Acho and Ricardo Guerra
CITEDI-IPN
2498 Roll Dr. 757 Otay Mesa San Diego, California, 92154 USA
Keywords:
Hysteresis, Dynamic Model, Friction.
Abstract:
This paper presents a dynamic hysteresis model; which is a modification of the well known LuGre model. This
model has been based on a modification to the LuGre model dynamic, which could be seen as a forward and
backward displacement in the steady state solution of the dynamic LuGre model. The LuGre friction model
is based on the average deflection of the bristles; implicitly, it is based on the relationship between stress and
strain of the bristles under deformation. From the friction model point of view, this dynamic hysteresis model
can capture the deformation behaviour between stress and strain beyond the elasticity region for the material
(the bristles), a region where the relationship between stress and strain is no longer linear. So, our model can
capture the friction phenomena of the original LuGre model and presents a new behaviour in the pre-sliding
regime. Simulation results are presented to support our contribution.
1 INTRODUCTION
While working in mechanical applications, it is im-
portant to have an accurate model of the system in
question. One of the more important considerations
that must be taken into account in any mechanical sys-
tem is the friction phenomenon. Many attempts have
been made to reproduce the effects caused by friction,
which is a non-linear effect. The importance of mod-
eling friction lies in the simple fact that all mechani-
cal systems present this phenomenon, moreover, be-
ing that it has non-linear behaviour, linear controllers
have very poor performance when trying to overcome
friction.
The first attempts made to model friction were sta-
tic models, such as the Coulomb model and the Vis-
cous friction model. The performance of these mod-
els was surpassed by the Dahl friction model (Dahl,
1968) and, more recently the LuGre friction model
published by Carlos Canudas et al. (C. Canudas de
Wit, 1995), which is at present one of the more widely
used models for friction compensation. It has the
ability to reproduce behaviours such as stick-slip mo-
tion, limit cycles, pre-sliding displacement and vary-
ing break away force. The basis for this model is an
abstraction that supposes the existence of microscopic
bristles on the surfaces in contact where friction is
present, these bristles are elastic and hence present
deformation which is captured in the model by the
introduction of an internal state which represents the
average deflection of said bristles. The interactions
between the bristles are responsible for the effects col-
lectively referred to as the friction phenomenon.
Research has been carried out to extend the LuGre
model but it relies on the usage of memory stacks
to reproduce the hysteresis phenomenon (J. Swevers,
2000). The main disadvantage of this approach is that
the hysteresis behaviour is modeled by a static func-
tion.
All the friction models presented recreate the elastic
behaviours of contact surfaces and the breakaway be-
haviours, but there is no model that can reproduce the
effects that occur between the elastic region and the
breakaway region, such as the segment of the stress-
strain curve (Young’s modulus and Hooke’s law) that
corresponds to non-elastic deformation region.
This paper presents a new dynamic hysteresis model
derived from the LuGre model. The inclusion of
the hysteresis friction model within the LuGre fric-
tion model yields results that approximate physical
closer to the reality than the previous models. The
new model shows a flat segment at the corners of the
pre-sliding displacement behaviour, produced by the
non-elastic deformation shown in Young’s modulus.
179
Benitez S., Acho L. and Guerra R. (2005).
DYNAMIC HYSTERESIS MODEL DERIVATED FROM LuGre MODEL.
In Proceedings of the Second International Conference on Informatics in Control, Automation and Robotics - Signal Processing, Systems Modeling and
Control, pages 179-183
DOI: 10.5220/0001156201790183
Copyright
c
SciTePress